Regular safety and quality inspections of docks can help protect them against damage and detect signs of decay, such as warped panels, cracked floors, and decayed wood. Look out for warped panels, cracked tiles, cracks in wood floors, or any other telltale signs.
Like wood, metal does not mix well with water, and rust can form on many parts of a dock over time, compromising its integrity and weakening it considerably. Failure to regularly replace these parts could also compromise its structural integrity and strength altogether. Contact Charleston Dock Works now!
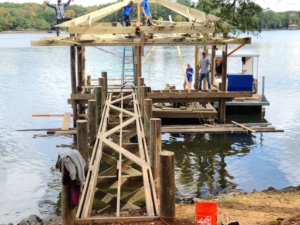
Floating structures used as moorings or docks pose a potential environmental risk since they are unregulated vessels and do not meet basic safety requirements. Their light construction makes them vulnerable to wind, wave, and storm loads, as well as colliding with other floating objects or being lost due to state laws requiring tracking devices. This could possibly lead to environmental contamination due to fractured floats leaving pieces behind that pollute nearby sea areas.
If a Member, master, or crew causes physical contact between their Ship and a fixed object that becomes lost at sea or sinks to the bottom, its owner could become responsible for various fees and costs related to charting, marking, raising, or removing it from its position on the seabed. Rule 37 provides cover for such expenses if there has been actual contact between both entities.
Leaks
Dock floats should be regularly examined for puncture holes. Puncture holes may occur from debris accumulation and leakage issues that require repair; particularly prevalent in areas that experience storms. A quick solution would be applying waterproof sealant over affected areas; in more serious instances it may be necessary to completely replace floats altogether.
Leaks in docks are usually caused by damaged hoses and cylinders that haven’t been addressed, leading to malfunctions of dock levelers and downtime. But these issues can often be avoided through regular maintenance and preventative measures like inspecting and cleaning before any damage occurs.
Long-term sunlight exposure can also cause floating docks exposed to it to lose their color and fade over time, becoming dull over time. While this may only be cosmetically detrimental, it should still be kept in mind that plastic bleaches over time. If this becomes an issue for your floating dock, providing shade or painting it might help restore it back to its former glory.
Owinging to their discreet nature, leaks in floating dock hull fittings are relatively easy to detect; typically taking the form of trickles or drips. To detect them quickly and effectively, dry off the area with paper towel before inspecting with flashlight and mirror for any wet spots on either the inside skin of the hull, rudder port, shaft log, stuffing box or fasteners that might indicate potential leakage issues. When applying chemical sealants or using plastic welding irons be aware that such tools can produce toxic fumes – work in well ventilated areas so as to minimize toxic fume emissions from such tools.
Cracks
Cracks in dock surfaces can be repaired by cleaning and drying the area affected, before applying an epoxy filler according to manufacturer’s instructions. Once set, this filler must be sanded until smooth; in cases of extensive cracking it may be necessary to completely dismantle and reassemble the dock itself.
Wood in contact with salt water can quickly decay, becoming susceptible to rot and decay. Replacing rotting boards with new lumber is typically an easy solution if only limited areas of damage exist; if major load-bearing areas of your dock have experienced rot, replacing it would likely be safer and ensure its structural integrity is preserved.
Concrete spall, or the break down of concrete surfaces due to exposure to extreme weather conditions such as rain, snow and ice exposure, is a common issue on loading docks. Forklift operators who must traverse these dock surfaces in order to access loading bays may find this particularly hazardous; however, regular inspection and repairs as needed can help prevent this type of damage from occurring.
Anti-slip coatings should also be added to the dock surface to enhance traction and lower risk of slips and falls, particularly in wet conditions. All docks should also undergo regular visual or professional inspection as part of an effective maintenance plan to detect potential issues before they become costly repairs; regular checks for cracks, warped boards, handrails, sagging, erosion or anything that might compromise its quality are also important considerations.
Wood Rot
Wood rot is caused by an organism called wood-rotting fungi which feed on moisture to decay the wood it infiltrates and demolish structures like window sills and door frames in homes – potentially dangerous when present on such vital elements as window sills and door frames that provide support.
Wood rot can be identified by blistered wood and peeling paint, followed by soft, punky wood that softens quickly as it decays further and spreads further inside your home. It should be dealt with immediately for best results.
To repair rotten wood, begin by scraping or chiseling away any damaged sections, cleaning the area thoroughly, applying wood restorer to help strengthen remaining timber sections, and creating an optimal base for filler application. Bondo wood filler should then be liberally applied before being sanded back for an inconspicuous repair that blends in seamlessly with surrounding timber sections. Prime and paint the area afterwards to protect it against further damage.
Keep a close eye on your dock to detect signs of wood rot before it becomes an expensive problem. If any early indicators such as peeling paint arise, take immediate steps to address them before they escalate further. Eliminate excess moisture by clearing gutters regularly and redirecting rain away from structures; treating repaired joists with fungicide as needed for repairs; inspecting wood surfaces regularly with high-quality polyurethane sealant applications; taking these proactive steps will extend its lifespan as well as help ward off costly repairs in the future.
Rust
If you notice rust on any steel components of your dock, sanding and paint can make them look brand new again. Rust can be hazardous; therefore it is wise to inspect your dock regularly and sand any areas affected by water. Keeping an eye out for signs of rust will allow you to detect problems early and save money by not needing to replace an entire dock system.
At the core of floating dock repair lies assessing damage and deciding if minor repairs or full replacement is required. Small cracks and wood rot may be remedied using plastic welding or silicone sealant repairs; if however, large-scale cracking threatens its integrity then replacement might be more suitable.
As soon as working with chemicals or in confined spaces, it’s imperative to wear appropriate protection in order to stay safe from their fumes and fumes that could potentially be hazardous to your health. Wearing slip-resistant shoes and gloves as well as a face mask with filters is necessary in order to filter any sealants or plastic welding iron fumes that might enter the atmosphere.
As part of your inspection, make sure all walking surfaces are free from splinters and in good condition. Anti-slip coatings may also help provide more traction on slippery walkways for improved traction in wet weather and to lower risk of slips and falls.
Checking all aspects of a dock, from its pilings and body frame to the pilings themselves, should also be part of this inspection process. A screwdriver can be used to look out for soft spots in wood that signal rot; any boards with damaged sections should be immediately replaced to avoid further structural damage to the dock’s structure; once these sections have been replaced with new boards treated with wood preservative to protect against future rot.